How-To Guide: Hazard Identification and Risk Assessment (HIRA)
- Michael Matthew
- 2 days ago
- 2 min read

Hazard Identification and Risk Assessment (HIRA) is a systematic approach to recognizing potential hazards in the workplace and evaluating the associated risks. Implementing HIRA effectively ensures the safety and well-being of employees and compliance with occupational safety regulations.
1. Understand the Importance of HIRA
HIRA is a foundational element of workplace safety programs. It aids in:
Preventing workplace injuries and illnesses
Complying with legal and regulatory requirements
Enhancing employee awareness and involvement in safety practices
Identifying opportunities for continuous improvement in safety managementWikipedia+17Santa Rosa County+17Home+17
2. Identify Workplace Hazards
Begin by systematically identifying potential hazards in the workplace. Hazards can be categorized as follows:
Chemical Hazards: Exposure to harmful substances such as solvents, adhesives, paints, and toxic dusts.
Physical Hazards: Conditions like excessive noise, radiation, heat, or vibration.
Biological Hazards: Exposure to infectious agents, molds, or animal materials.
Ergonomic Hazards: Tasks involving repetitive motions, heavy lifting, or awkward postures.
To identify these hazards:
Review Safety Data Sheets (SDS) and product labels for chemical information.
Conduct workplace inspections to observe physical conditions and work practices.
Consult with employees to gather insights on potential hazards they encounter.
Analyze incident reports, near misses, and medical records for patterns indicating underlying hazards.
3. Assess the Risks
Once hazards are identified, assess the risks associated with each by considering:
Likelihood: The probability of the hazard causing harm.
Severity: The potential impact or consequence of the hazard.
Use a risk matrix to classify risks as low, medium, or high, which aids in prioritizing control measures.
4. Implement Control Measures
Apply the hierarchy of controls to mitigate identified risks:
Elimination: Remove the hazard entirely from the workplace.
Substitution: Replace the hazard with a less dangerous option.
Engineering Controls: Isolate people from the hazard through design modifications.
Administrative Controls: Change work procedures to reduce exposure to hazards.
Personal Protective Equipment (PPE): Provide protective gear to employees as a last line of defense.
5. Monitor and Review
Regularly review and update the HIRA process to ensure its effectiveness:
Conduct periodic workplace inspections and audits.
Reassess risks when changes occur in processes, equipment, or personnel.
Encourage continuous feedback from employees regarding safety concerns.
Document all findings and actions taken for accountability and future reference.
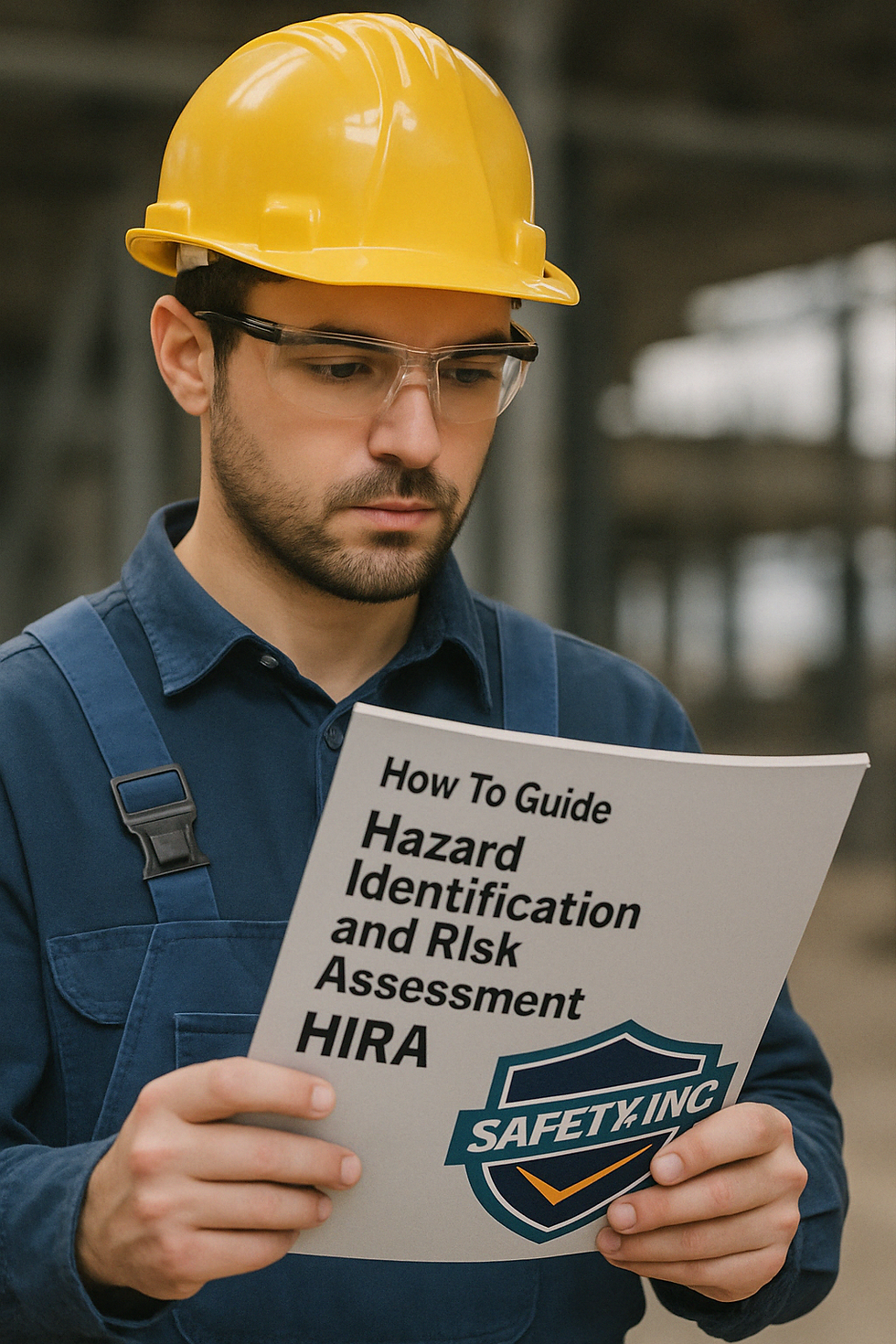
References
Occupational Safety and Health Administration. (n.d.). Safety Management - Hazard Identification and Assessment. Retrieved from https://www.osha.gov/safety-management/hazard-identification
SafetyCulture. (n.d.). Hazard Identification and Risk Assessment: A Guide. Retrieved from https://safetyculture.com/topics/risk-assessment/hazard-identification-and-risk-assessment/
Public Health Ontario. (2020). HIRA Worksheet Template. Retrieved from https://www.publichealthontario.ca/-/media/documents/h/2020/hira-worksheet-template.pdfOSHASafetyCultureOntario+3Public Health Ontario+3Public Health Ontario+3
By diligently following these steps, organizations can create a safer work environment, reduce the likelihood of incidents, and promote a culture of proactive safety management.
We Can Help! If you need assistance in determining your workplace hazards contact Mike@SAFETY.INC
Comments