Loading Dock Safety: A Practical Guide to Preventing Incidents
- Michael Matthew
- 2 days ago
- 19 min read

Introduction
Loading docks are high-risk zones in any warehouse or manufacturing facility. With forklifts, heavy loads, and tractor-trailers all converging in one area, the potential for accidents is significant. In fact, about 25% of all warehouse injuries occur on the loading dock, and for every recorded accident there may be dozens of near-misses capstonelogistics.com.
Common incidents include forklift roll-offs, employees struck by backing trucks, and falls from elevated dock ledges. The consequences can be severe – damaged goods, costly downtime, regulatory penalties, and most importantly, serious injuries or loss of life.
This safety guide provides a comprehensive checklist of best practices to maintain a safe loading dock environment. A proactive approach to loading dock safety not only protects workers but also improves efficiency and prevents costly disruptions. Each section below expands on critical safety checkpoints with examples and industry best practices. By reinforcing these principles, warehouse managers, safety trainers, and frontline dock workers can work together to minimize hazards. Always remember: no deadline or shipment urgency is worth compromising safety.
Maintaining Loading Dock Safety
A clean, well-organized dock area is the foundation of safety. Clutter, poor lighting, and faulty equipment can turn an ordinary task into a dangerous incident. Maintaining a safe dock environment means keeping the physical workspace free of hazards and ensuring all equipment is in proper working order. Key practices include:
Housekeeping and Spill Management: Keep the loading dock floor clean, dry, and free of debris at all times. Promptly clear away shrink wrap, broken pallets, or spilled liquids to prevent slips and trips. For example, if a pallet load breaks and scatters product, rope off the area and clean it immediately before work continues. A regular cleaning schedule should be in place, especially during bad weather when rain or snow can be tracked in and make floors slick. Anti-slip mats or grit tape can be applied in areas prone to moisture.
Lighting and Visibility: Ensure the dock area is well-lit, including both indoor dock bays and outdoor truck approach areas. Burned-out lights should be replaced promptly to eliminate dark spots. Adequate lighting helps forklift drivers and spotters see obstructions and helps truck drivers align trailers accurately after dark. Consider installing motion-sensor lights or extra illumination at each bay if current lighting is insufficient. Paint or mark the dock edges with high-visibility yellow paint so that the boundary of the loading bay is always clearly visible to workers. Good visibility is a simple but crucial deterrent to accidents.
Dock Door and Edge Safety: Treat an open dock door like any other ledge at height – fall protection is required. OSHA regulations mandate protective measures (such as guardrails, safety chains or gates) for any drop of 4 feet or more southflorida.assp.org. Install sturdy removable dock gates or safety chains across open dock doors when no trailer is present. This prevents employees or equipment from accidentally rolling off the edge. Likewise, ensure dock drop-off areas are not used as pedestrian walkways unless proper guardrails are in place. Many facilities also use visual warnings like floor stripes or signage reading “CAUTION – DOCK EDGE” to remind staff of the fall hazard.
Equipment Inspection and Maintenance: All dock equipment should be regularly inspected and kept in good repair. This includes dock levelers, dock plates, bumpers, seals, and overhead doors. Before each shift, do a quick check: is the dock leveler operating smoothly without excess bouncing? Are dock plates free of cracks and securely placed? Do rubber dock bumpers (which absorb trailer impact) remain intact and firmly mounted to the dock face? Repair any defect promptly – a malfunctioning dock plate or door can lead to downtime or injury. Likewise, forklifts and pallet jacks used on the dock must undergo daily inspections (brakes, tires, controls) and scheduled maintenance. Never use a forklift with known mechanical issues on a loading dock; a sudden brake failure on a dock could be catastrophic.
Maintaining a safe dock environment requires vigilance and teamwork. Encourage all employees to take ownership of the area – if they see a spilled oil patch or a loose dock plate lip, they should report it or address it immediately. By keeping the workspace orderly and equipment reliable, you create a solid groundwork for all other safety measures to be effective.
Managing Truck Traffic
Loading docks often see a continuous flow of truck movement – trailers backing in, pulling out, or idling during loading. Managing truck traffic is critical to prevent collisions, confusion, and catastrophic accidents. This involves controlling how trucks enter, park, and exit the dock area, as well as coordinating between drivers and dock workers. Best practices for truck traffic management include:
Traffic Control Plans: Establish and enforce a clear traffic management plan for the facility. This plan should designate specific routes, speeds, and procedures for trucks. For instance, post a low speed limit (such as 5 mph) for all vehicles in the yard and use speed bumps or clearly marked signs to ensure compliance. Designate one-way traffic flow where possible to reduce the need for complex maneuvering. If multiple docks are in use, consider a schedule or communication protocol so that only one trailer moves at a time while others remain stationary.
Visual Communication Systems: Utilize dock traffic lights and signals to communicate with driverscapstonelogistics.com. Red/green light systems at each bay are an effective way to indicate when a truck is cleared to back in or pull out. For example, a common system keeps a red light facing the truck driver (meaning “stop, do not move”) while loading is in progress, and switches to green only when it is safe for the driver to depart. Inside the dock, a corresponding light can signal to forklift operators when it’s okay to enter the trailer. These visual cues reduce the chance of miscommunication. If electrical signal systems are not in place, use hand signals or sign boards consistently – all drivers and dock staff should understand the signals for stop, all-clear, etc.
Spotters and Mirrors: For facilities with tight yards or blind spots, use trained spotters to guide trucks into position. The spotter should wear high-visibility attire and stay in the truck driver’s mirror view at all times, using agreed-upon hand signals. Convex mirrors at blind corners and dock exits can also help drivers see forklifts or pedestrians before it’s too late. In rainy or foggy conditions, be even more cautious with guiding trucks, as visibility and braking distance are affected.
Traffic Rules and Enforcement: Enforce strict parking brake and engine shut-off rules for trucks at the dock. As soon as a trailer is positioned at the bay, the driver should put the vehicle in park, set the parking brake, and if required, turn off the engine (this also helps prevent exhaust buildup). Some companies require drivers to hand over the keys to a supervisor during loading as an extra precaution against an unintended departure. Ensure drivers know they must not move the truck until explicitly instructed by dock staff. Likewise, institute a “no unauthorized truck movement” policy: yard trucks or hostlers should not re-position trailers without clearance. Any violations of these traffic rules should be addressed immediately – consistent enforcement underscores how vital they are for safety.
Effective truck traffic management reduces the likelihood of deadly mishaps such as drive-offs or trailers striking individuals. It also minimizes property damage (for example, collisions with dock doors or other vehicles). By clearly directing the flow of trucks and using tools like lights and spotters, you create an orderly, safe approach to the loading dock that protects everyone on site.
Ensuring Smooth Loading and Unloading Operations
Once a trailer is parked safely at the dock, the focus shifts to the loading and unloading process itself – essentially the transfer of goods between the trailer and the facility. This is where forklift operators, pallet jacks, and manual laborers interact closely with heavy loads and equipment. Ensuring smooth loading and unloading operations means handling materials efficiently without compromising safety. It involves using the right equipment properly and following procedures that prevent falls, tip-overs, or product damage. Consider the following best practices:
Dock Levelers and Bridges: Before loading begins, secure the dock leveler or bridge plate between the dock and the trailer. Ensure it’s properly extended and locked in position so there is a smooth, even surface for forklifts to travel across. Verify that the plate’s weight capacity exceeds the combined weight of the forklift and load. If your dock uses portable dock plates or boards, make sure they are placed correctly with no gap and are anchored or locked to prevent shifting. Never start driving a forklift into a trailer until the dock leveler or plate is confirmed stable. If a trailer is parked too high or low relative to the dock, use adjustable ramp solutions or properly rated load boards rather than risky improvisation. A secure connection between trailer and dock will prevent sudden separations or gaps that could catch a wheel.
Trailer Inspection and Support: Inspect the trailer’s interior and floor condition before any forklift enters. Dock workers should verify that the trailer floor is structurally sound with no rot, cracks, or holes that could give way under the weight of a lift truck. If there are concerns (e.g., a soft wood floor or damaged sections), unload that trailer manually or with lighter equipment to avoid a collapse. Additionally, confirm the trailer’s landing gear is down and locked if the tractor has detached. For extra safety with an unsupported trailer, use a trailer jack stand under the nose of the trailer to prevent it from up-ending when heavy forklifts drive to the front. This simple step can avert a dangerous tip-over incident.
Safe Forklift Operation: Operating forklifts on docks and inside trailers requires special caution. Forklift drivers must drive slowly and carefully when on a dock plate or inside a truck. Sudden braking or accelerating can cause the trailer to shift or the dock plate to dislodge. Maintain a safe distance from the edges of the dock – never turn or approach too close to an open edge, as forklifts can tip or fall off. A best practice is to keep the forklift’s steering wheels further back from the edge and only the front wheels on the plate when entering a trailer, minimizing exposure to the drop-off. Remember that trailers can experience “dock walk” or trailer creep (gradually moving away from the dock due to the forklift’s momentum). Even with wheel chocks or restraints in place, check the gap periodically. If the gap widens, stop operations and re-secure the trailer. Communication is also key: forklift operators should sound the horn before exiting the trailer or going in reverse out of a truck, alerting anyone nearby.
Load Handling and Stability: Whether using forklifts or pallet jacks, ensure that loads are stable and secure before moving them. Stack pallets squarely and shrink-wrap if necessary so boxes won’t topple. When breaking down a load, take care that remaining items on the pallet or in the trailer are left stable (e.g., don’t leave a heavy box teetering on the edge of a stack). Use load straps or bars inside trailers to prevent freight from shifting in transit and potentially falling when doors open. If pallets are heavy or awkward, use team lifting or lift assist devices to unload safely rather than one person straining. The goal is to avoid any sudden shifts or drops during the transfer process that could injure workers or damage goods.
Ergonomics and Efficiency: “Smooth operations” also means looking after the well-being of workers doing physical loading. Train employees in proper lifting techniques for manual handling to prevent back injuries. Provide materials handling aids (carts, pallet jacks, conveyors) to minimize carrying loads by hand. Organize loads and staging areas so that workers do not have to overreach or twist awkwardly when moving products. An efficient layout – for example, having receiving paperwork and pallet space ready before the truck arrives – can reduce chaotic rushing. Never encourage dangerous shortcuts like “dock jumping” (jumping off the dock to the ground) – stairs or ladders should be used to get on and off the dock safely. By planning the loading/unloading tasks and equipping staff properly, you maintain both speed and safety.
By paying attention to these practices, loading and unloading can be done quickly and safely. Smooth operations are not just about productivity – they also mean that every step of the process has been thought out from a safety perspective. Consistency in following these procedures will greatly reduce incidents such as pallet accidents or forklift mishaps during the critical transfer of goods.

Securing Vehicles at the Dock
One of the most dangerous moments on a loading dock is when a trailer unexpectedly moves or separates from the dock while workers are still loading or unloading. Securing vehicles at the dock is therefore a top priority. This involves using physical restraints or chocks to immobilize trucks and trailers so they cannot budge an inch until work is finished. Failure to secure a trailer can lead to devastating “trailer creep” or premature departure incidents – for example, a forklift can fall through the gap if a trailer pulls away even a short distance lillyforklifts.com. The following measures will ensure every vehicle at your dock stays put until you’re done with it:
Wheel Chocks and Restraints: Always chock trailer wheels firmly on both sides or engage an automatic vehicle restraint system (dock lock) before any loading/unloading begins. Chocks should be high-quality, intended for the size of tire, and placed snugly against the wheels. It’s a good practice to double-check chocks after placement – give them a kick or tug to ensure they won’t slip. Many warehouses paint a rectangular outline on the pavement showing where chocks should go, as a constant reminder. If using an automated dock lock (a hook that clamps onto the trailer’s rear impact guard), verify that the lock indicator shows it’s properly engaged. Do not allow any forklift entry into a trailer until the truck is confirmed secured. As management, set a policy that every trailer must be restrained — no exceptions. This is critical even for “quick jobs” or if the driver insists they’ll hold the brake; complacency leads to accidents.
Trailer Parking Brakes: In addition to chocks or restraints, ensure the driver sets the vehicle’s parking brakes and/or air brakes. Redundant measures are encouraged – the combination of wheel chocks and brake application provides multiple layers of security. If an air brake leak occurs or a chock slips, the other measure still holds the trailer. Many companies include a step in their standard operating procedure for a dock worker or yard hostler to visually confirm that trailer brake lines are disengaged (which activates the trailer spring brakes) once the trailer is parked.
Communication with Drivers: Implement a clear communication protocol with truck drivers regarding vehicle security. For example, use a safety checklist that a driver must sign off on upon arrival, confirming: “Wheels chocked, engine off, keys surrendered (if applicable).” Only after that does the dock light turn green or the dock door open. Conversely, the driver should know they are not allowed to re-enter the vehicle or start the engine until loading is complete and they have been given explicit permission to depart. Some facilities use a “dock lock engaged” sign or a physical lockout tag hung on the driver’s window as a visible indicator. Good communication prevents any confusion – the driver and the dock team all understand that the trailer is off-limits for moving.
Preventing Trailer Separation: Even with wheels chocked, trailers can shift if their support fails or if they are improperly positioned. Inspect the trailer’s alignment and support before and during the job. The trailer should be snug against the dock bumpers; if there is a gap, a trailer can gain momentum and jump the chocks. If a trailer is not firmly contacting the dock or the dock lock cannot engage properly (for instance due to mismatched trailer guard height), stop and resolve the issue – perhaps by re-positioning the trailer or using alternate securing devices. For spotted (dropped) trailers, as mentioned earlier, always use landing gear jack stands as additional support. This prevents the trailer’s nose from dropping or collapsing under load. Keep in mind that trailers with air suspension can gradually lower as air bleeds, so periodic checks are wise.
After-Loading Departure: Only when all personnel, forklifts, and materials are clear of the trailer should the restraint be removed or wheel chocks pulled. Establish a sequence: for example, the dock worker gives a thumbs-up to a supervisor, who then deactivates the dock lock and switches the exterior light to green (or gives the driver the keys back). This disciplined process ensures there is no mistake about when it’s safe for the truck to depart. Under no circumstances should a driver pull out if any uncertainty remains about someone possibly still in the trailer or on the dock plate.
Securing every vehicle that comes into your dock is non-negotiable. The cost in time is minimal – a minute to set wheel chocks – but the action can literally save lives. Numerous tragedies have occurred from trailers creeping or driving off with people still inside; using restraints and following protocol will eliminate almost all “trailer pull-away” incidents from your operation. It is a simple, powerful safety step that every dock should religiously uphold.
Controlling Pedestrian Access
Loading docks are primarily vehicle and equipment work zones, and anyone on foot is especially vulnerable. “Pedestrians” include not only visitors or other employees passing through, but also the dock workers themselves when they are not on forklifts. Controlling pedestrian access means keeping people who are on foot safely separated from the dangers of forklifts, pallet movement, and truck traffic. It also means protecting people from falling off dock edges or entering areas where they shouldn’t be. Here are important strategies to manage pedestrian safety:
Restrict Access to the Dock Area: Physically limit entry to active loading docks to only those who have a job to do there. Use barriers and signage at all entrances to the dock zone – for example, a swinging gate or chain across a hallway leading to the dock, with a sign “Authorized Personnel Only – Loading Dock in Operation.” This prevents random foot traffic or curious visitors from wandering into a hazardous area. If your facility layout requires pedestrians to pass near docks (for instance, a corridor that crosses the dock bays), consider re-routing foot traffic or scheduling non-intersecting times. Some warehouses paint a bright red line on the floor a few meters away from the dock openings and require that no one on foot crosses that line while a trailer is being serviced.
Designated Walkways and Markings: Clearly mark pedestrian walkways in any areas where workers on foot and equipment might intersect. Using high-visibility floor tape or durable paint, create pathways with striped lines or different floor colors. These lanes signal where it is safe for people to walk and where it is off-limits. For example, you might outline a path from the warehouse interior to the dock office that stays well clear of all dock doors. Crosswalk-style markings can indicate where a person might need to cross a forklift lane – at those crossings, add floor text like “STOP – LOOK FOR FORKLIFTS.” The goal is to provide visual cues so that pedestrians stick to safe zones and forklift drivers know where to expect foot traffic. According to best practices, pedestrians in dock areas should be trained to stay within designated aisles or zones marked for foot traffic safesitehq.comsafesitehq.com.
Pedestrian Awareness and PPE: All individuals who work near loading docks should wear appropriate high-visibility apparel, such as reflective vests or bright-colored uniforms. High-vis clothing makes it easier for forklift operators and truck drivers to spot people moving in their peripheral vision or in dim conditions. Additionally, insist on basic personal protective equipment: steel-toe boots to prevent foot injuries from dropped objects, and hard hats if overhead hazards exist (for example, if using overhead cranes or if items could fall from racks during loading). While PPE is the last line of defense, it’s an important one. Furthermore, teach dock workers to practice situational awareness: for example, never assume a truck driver or forklift operator sees you – try to make eye contact or signal your presence. If a pedestrian must approach a trailer or step into a lane, they should get acknowledgment from the equipment operator first.
Barrier Systems and Fall Protection for People: We’ve discussed gates at dock edges under the environment section, which are crucial when a door is open. In addition, consider using pedestrian guardrails or bollards to separate walkways from forklift paths. For instance, guardrails can fence off a pedestrian break area or time clock that’s near the dock, so that even if a forklift loses control, the barrier provides protection. Where practical, use swing gates or warning chains across dock openings whenever a trailer is not present, to prevent anyone from accidentally stepping off the ledge. Some facilities even install visual/audible alarms that trigger if someone crosses into a truck lane unexpectedly (motion sensors that announce “Caution, person approaching” to forklift drivers). The level of control should match your operation’s risk – a busy distribution center might need more robust pedestrian barricades than a small loading area.
No Pedestrians During Active Loading: A good rule is to prohibit on-foot entry to a trailer or within a certain radius of a forklift while loading/unloading is underway, except for the trained loading team. For example, if an office clerk needs to check cargo inside a trailer, they should wait until the forklift driver exits and turns off the machine. Similarly, truck drivers should stay in a designated safe spot (like a driver waiting area or inside their cab if permitted) rather than walking around the dock while forklifts are moving. Minimizing the mixing of pedestrians and moving equipment at the dock greatly reduces the chance of struck-by injuries.
By engineering the workspace with clear walkways, barriers, and rules, you create a safer environment for pedestrians. Remember that in any contest between a person and a piece of heavy equipment, the person will suffer – so the goal is to eliminate that interaction except when absolutely necessary. Through training, signage, and physical safeguards, workers on foot can be kept out of harm’s way during loading dock operations.

Training and Continuous Improvement
Even the best safety checklist is only as effective as the people following it. That’s why a culture of continuous training and improvement is essential for loading dock safety. In this sixth section, Training and Continuous Improvement, we focus on building knowledge, reinforcing safe practices, and constantly evaluating how to make the dock safer over time. Safety is not a one-time effort – it’s an ongoing process of education, practice, review, and enhancement. Here are our recommendations for fostering continuous safety excellence:
Comprehensive Employee Training: All employees who work on or around loading docks should receive thorough initial training on dock safety procedures. This includes classroom or toolbox talk instruction on the hazards of the job (e.g., forklift dangers, fall risks, pinch points) and practical demonstrations of the correct procedures (such as how to chock wheels properly, how to operate dock levelers, and the signals used between spotters and drivers). For example, new hires might spend their first day learning the safety checklist and watching senior staff perform a supervised trailer loading, before they ever operate equipment themselves. Make sure to cover emergency procedures too – what to do if an injury occurs, who to call, where the emergency shut-offs and first aid kits are located. Forklift operators must be certified as required by OSHA, and their training should emphasize dock-specific scenarios like approaching a trailer, maintaining dock edge distance, etc. Don’t assume a licensed forklift driver knows these nuances; train them for your environment.
Regular Refreshers and Drills: Schedule periodic safety refresher sessions for all dock workers. Over time, people can become complacent or forget details, so refreshing their knowledge is critical. These could be quarterly safety meetings where a different topic is reviewed (one meeting on pedestrian safety, another on securing trailers, for instance). Incorporate hands-on drills as well: you might simulate an emergency – such as a forklift tipping scenario or a fire on the dock – and have the team practice the response (evacuation, using a fire extinguisher, etc.). Drills build muscle memory so that in a real crisis, responses are quick and correct. Some companies hold annual “safety rodeos” or competitions to reinforce forklift skills and safe loading techniques in a fun, engaging way. However you do it, make ongoing training an expected part of the job. It sends the message that safety is never “one and done,” but a continuous learning process.
Supervision and Coaching: Encourage supervisors and experienced employees to coach in real time on the dock. A safety manager or dock supervisor should routinely observe operations and give immediate feedback or correction when they see unsafe behavior or a missed step. For example, if a worker forgets to put on the dock safety chain, the supervisor should stop the process and use it as a teaching moment, not just quietly fix it for them. This on-the-job coaching helps reinforce training in a practical context. Consider implementing a “safety mentor” system where each new dock worker is paired with a veteran who models the right safety habits. Positive reinforcement is important too – recognize and commend employees when they proactively follow safety procedures or suggest improvements. Building a team mindset where workers look out for each other’s safety is the ultimate goal.
Audits and Inspections: Conduct regular safety audits of the loading dock operations. This could be a formal monthly inspection by a safety committee or an external auditor who checks compliance with all the points in this guide. Use a checklist (like the one this guide expands upon) and verify that each item – from wheel chock usage to housekeeping – is being maintained. Note any deficiencies and investigate why they occurred. Maybe you’ll find, for instance, that wheel chocks are often not used on a certain shift – further inquiry might reveal those chocks are damaged or there’s a misconception about their necessity, which you can then address through repair and retraining. Treat audits not as a “gotcha” exercise but as a tool for continuous improvement. Share the findings with the team and collectively brainstorm solutions for any issues found.
Incident Reviews and Feedback Loop: If an accident or near-miss does occur at the dock, treat it as a critical learning opportunity. Immediately secure the area and tend to any injuries first. Then, perform an incident investigation to understand the root causes. Was a procedure not followed? Was there an unforeseen hazard? Engage workers in this process; often those on the ground have valuable insights. Once you determine causes, update your safety protocols or training to prevent a repeat. For example, if a near-miss happened because a trailer creep wasn’t noticed in time, you might institute a new rule that two people must verify chocks and periodically re-check them during loading. Also establish a simple system for employees to report hazards or near-misses anonymously if needed. When workers report that a dock lever is sticking or that they had a close call with a pedestrian, respond quickly and thank them – this openness can avert future accidents.
Stay Current and Strive for Improvement: Safety standards and technologies evolve. Stay up-to-date with industry best practices, OSHA regulations, and new safety equipment on the market. For instance, if new trailer restraint technology or advanced sensor systems are available, evaluate if they could enhance your dock safety. Network with industry peers or join safety associations to learn from others’ experiences. Periodically review whether your safety goals are being met (e.g., reduction in incidents, audit scores improvement). Set new goals to drive further improvement. By fostering an attitude that “we can always improve safety”, you prevent complacency from taking hold.
In summary, training and continuous improvement efforts create a safety culture that underpins all the specific rules and procedures. Workers who are well-trained, alert, and engaged will naturally operate more safely and catch problems early. Companies that invest in this ongoing education and feedback process tend to have significantly fewer accidents and a more confident, safety-conscious workforce. Make loading dock safety training a living program – one that grows and adapts with your operation.
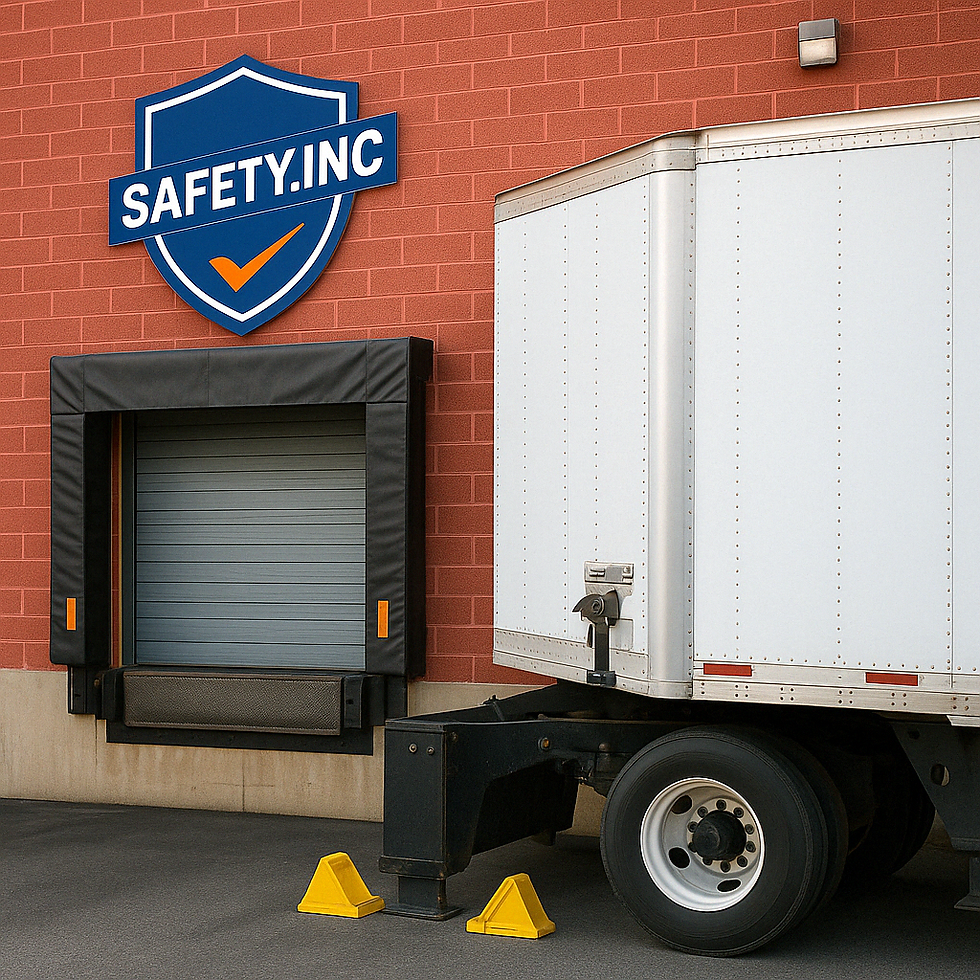
Conclusion and Call to Action
Loading dock safety is everyone’s responsibility, from upper management to the newest hire on the floor. This guide has covered the core pillars – maintaining a safe environment, managing vehicle traffic, handling loads carefully, securing trailers, protecting pedestrians, and continuous training – but a document alone doesn’t save lives. Action is what makes the difference. We urge you to take the following steps starting today: conduct a walk-through of your loading docks with this checklist in hand, involve your team in identifying any weaknesses, and commit to implementing at least one improvement immediately.
No matter how busy operations get, never prioritize speed or convenience over safety. An incident can cost far more in human and financial terms than the few minutes saved by a shortcut. Ensure your company’s leadership actively supports safety upgrades – whether that means investing in better dock barriers, scheduling extra training sessions, or hiring an extra spotter during peak shifts. Create an environment where workers feel empowered to speak up about hazards and where safety protocols are not just rules, but the routine way of doing business.
In closing, make loading dock safety a core value of your organization. Review your current protocols, update them to reflect best practices, and regularly revisit them for improvements. Set the tone that every shift should begin with safety in mind and end with everyone going home unharmed. By following the guidance in this safety handout and fostering a culture of vigilance and respect, you can dramatically reduce risks at your loading docks. The time to act is now – assess your loading dock safety measures and take proactive steps to elevate them. Your employees’ lives and your company’s success depend on it. Stay safe and stay committed to continuous improvement in loading dock safety!
Comments